7 mars 2023
Votre entreprise est-elle prête pour la robotique collaborative?
La robotique collaborative est l’une des grandes tendances en automatisation, notamment parce qu’elle augmente la compétitivité des entreprises. Elle tend aussi à améliorer leur capacité de production, tout en libérant du personnel pour réaliser des activités à plus grande valeur ajoutée. Avant de vous lancer, on vous propose de regarder sept étapes clés.
Depuis 2021, l’entreprise Radius Automatisation industrielle propose des cellules robotisées qu’elle conçoit, fabrique et intègre à partir de Trois-Rivières. « Les entreprises qui nous contactent veulent savoir si la robotique collaborative peut les aider ou encore s’il existe un poste de travail dans leur usine qui se prêterait bien à l’automatisation », explique Sébastien Cloutier, son fondateur. Une visite des installations permet alors de cibler ou de valider les applications qui ont le plus fort potentiel de robotisation.
« Il arrive aussi qu’un poste de travail ait déjà été ciblé par l’entreprise avec l’intention de prévenir des blessures ou d’offrir des conditions plus favorables au personnel en place », continue-t-il. Peu importe ce qui initie votre intérêt pour la robotique collaborative, l’application souhaitée, les compétences de votre équipe ou les objectifs poursuivis, il existe des étapes en vue de préparer son entreprise à accueillir son premier robot collaboratif.
En voici quelques-unes.
7 étapes pour intégrer un robot collaboratif
1. Réunir une équipe à l’interne
Un projet d’automatisation est une occasion propice pour regrouper différentes expertises déjà présentes au sein de votre équipe. En réunissant dès les premières réflexions les responsables de la production, de la qualité ou la direction de l’entreprise par exemple, ainsi que les personnes aux opérations qui réalisent actuellement les tâches et qui pourraient être affectées par leur automatisation, vous obtenez un plus grand potentiel de réussite.
Même si ça prend parfois un peu plus de temps au départ pour partager une vision commune du projet, ne dit-on pas qu’ensemble on va plus loin? En effet, chaque personne sera appelée à amener ses connaissances, ses compétences et sa perspective unique quant au projet. Puis, après un certain moment, on voudra répondre aux questions suivantes : Qui tient-on informé de l’avancement de la cellule robotisée? Qui en sera responsable? Qui va la réaliser? Quels espaces de collaboration se donne-t-on pour y arriver ensemble?
2. Confier le projet à un intégrateur ou le réaliser à l’interne
Un intégrateur robotique, c’est celui qui s’assure de regrouper les sous-systèmes d’une cellule robotisée dans le respect des fonctionnalités demandées. Sa plus-value réside, entre autres, dans sa connaissance fine des spécificités de chaque composante, de leur fonctionnement et de leur interopérabilité et de leur compatibilité avec vos équipements. Selon votre situation, le choix de vous tourner vers l’externe ou l’interne pour réaliser votre projet en automatisation pourrait dépendre de plusieurs facteurs.
En général, un intégrateur robotique vous propose une solution clé en main à un coût forfaitaire. En étant à l’extérieur de votre entreprise, un temps lui sera nécessaire pour prendre connaissance de vos processus manufacturiers. Malgré cela, l’expérience qu’il a su tirer des nombreux projets réalisés va tendre à accélérer la mise en route de la cellule robotisée, vos gains de productivité et votre retour sur investissement. Quoi qu’il en soit, vous devriez vous assurer que votre équipe soit adéquatement formée pour opérer et entretenir votre nouvelle solution pour maximiser votre autonomie.
Un projet réalisé exclusivement à l’interne pourrait vous permettre d’atteindre vos objectifs à plus faibles coûts. Néanmoins, malgré que les membres de votre équipe soient en mesure d’apprendre à utiliser et à programmer un robot collaboratif, c’est possible que cela empiète sur leurs autres responsabilités en lien avec les activités courantes. Ainsi, il peut être sage de dégager du temps au sein de l’équipe pour traverser les essais-erreurs liés à la nouveauté et vivre une expérience optimale avec la robotique collaborative.
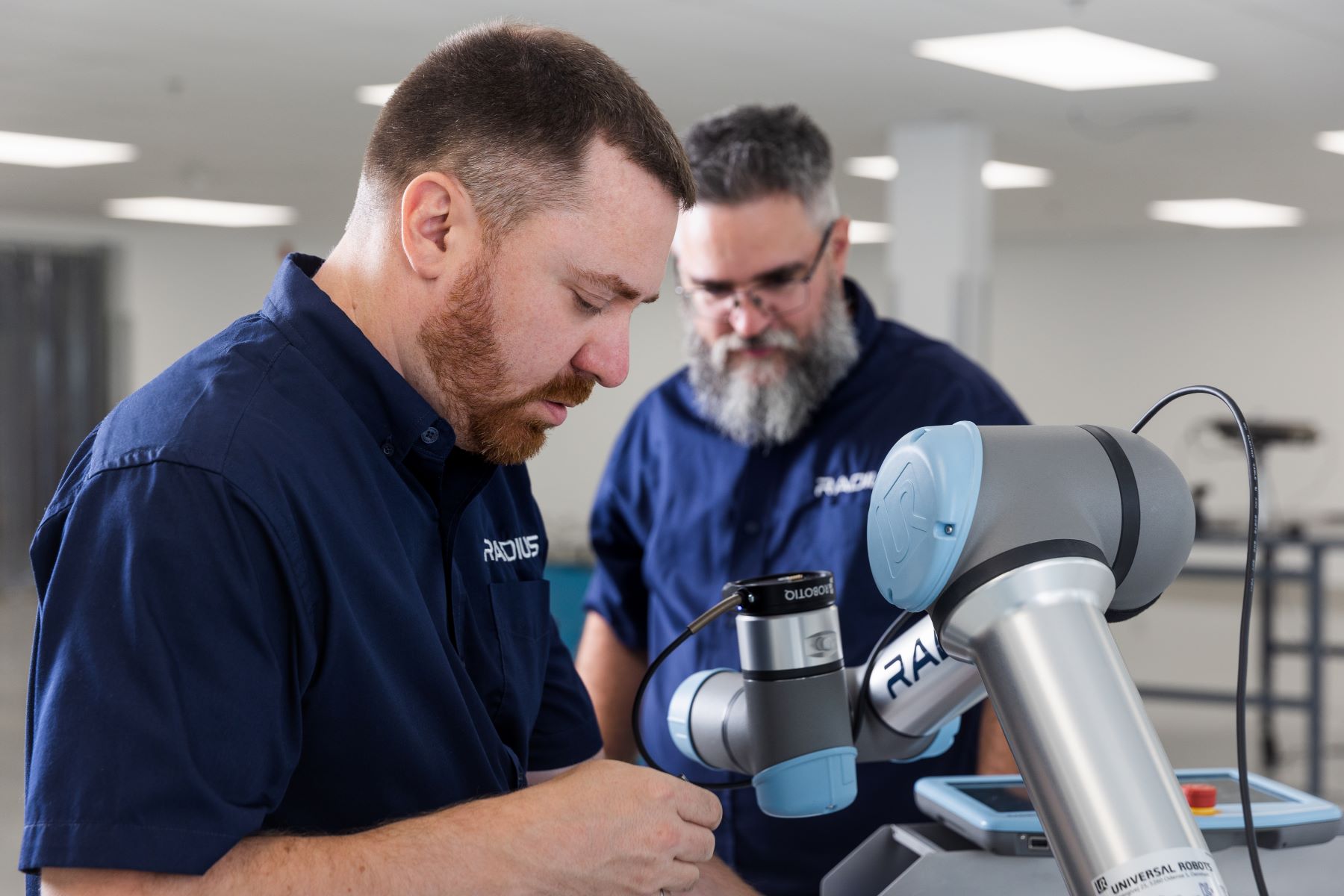
Installation d’une caméra et d’un préhenseur sur un bras robotisé
3. Choisir la tâche à automatiser
Selon la stratégie qui vous amène à considérer l’automatisation pour votre entreprise, vous pourriez sélectionner une tâche plutôt qu’une autre. Ici, les choix ne manquent pas!
Voici quelques exemples pour vous guider :
- Pour libérer du personnel aux opérations, on regardera du côté des tâches répétitives, sans valeur ajoutée, dangereuses ou démotivantes qui peuvent être sources d’absentéisme, de départs ou de vos défis de recrutement de la main-d’œuvre.
- Pour augmenter votre capacité de production, on tentera d’augmenter le rendement global, en maintenant une bonne cadence de production, en évitant les arrêts inutiles ou les goulots ou en produisant plus longtemps, la nuit par exemple.
- Pour implanter une culture d’innovation et d’amélioration continue, on choisira d’automatiser une première tâche avec l’intention de bâtir l’expérience de votre équipe, afin de relever dans l’avenir des défis à fort impact et de plus en plus complexes.
4. Découper la séquence de production en étapes
À mesure que le projet d’automatisation se précise, il devient à nouveau essentiel de réunir l’équipe pour se donner une vue complète de la séquence de production à robotiser. Chaque sous-étape devient une occasion de se demander comment tirer parti des forces du robot et de l’être humain. On propose aussi de tenir compte du poste de travail qui constitue l’étape suivante pour connaître ce qui peut ajouter de la valeur comme une disposition particulière des pièces, une cadence de travail ou encore l’état de propreté des pièces reçues.
5. Identifier les critères de succès du projet
Plusieurs questions sont ici essentielles, la principale étant la suivante : Quel est notre objectif principal? Votre réponse pourrait entre autres être d’améliorer votre productivité, votre capacité de production, la qualité de vos pièces, l’ergonomie d’un poste de travail, la gestion ou la valeur de votre inventaire ou encore l’utilisation optimale de vos ressources humaines. Selon l’objectif recherché et la direction établie, quelques indicateurs clés de performance (ou « KPI ») ou des seuils de réussite pourraient être choisis.
« Une entreprise a récemment fait appel à nous pour augmenter la capacité d’un processus d’emballage en fin de ligne », explique M. Cloutier. « La cible de mise en boîte a été établie par l’équipe à 200 bouteilles par minute, ce qui devait permettre de libérer 5 personnes dont c’était la tâche », ajoute-t-il. En établissant tôt ce critère de succès, tout le monde s’offre une base commune pour concevoir une solution satisfaisante, évaluer la réussite du projet et contribuer plus tard à son amélioration continue.
6. Élaborer un concept général
À cette étape, il s’agit de développer un concept viable et fiable avec juste assez de caractéristiques (et pas plus) pour satisfaire les indicateurs ou les seuils de réussite établis. Certaines sous-composantes peuvent être testées ici pour diminuer l’incertitude du concept, avant de lancer le « Go ». Une approche Lean et agile permettra d’implanter rapidement une cellule robotisée fonctionnelle, ce qui va accélérer le retour d’information des équipes en place. L’idée est d’arriver à progresser vers une cellule finale sans avoir à revenir en arrière.
« Avec la cible de 200 bouteilles par minute en tête, notre équipe s’est orientée vers un design permettant au robot collaboratif de prendre 24 bouteilles en même temps grâce à l’ajout d’un système d’aiguillage sur le convoyeur. Les bouteilles peuvent ensuite être directement déposées dans une boîte pour l’emballage », souligne-t-il. Les personnes libérées de cette tâche peuvent maintenant opérer un autre équipement, s’occuper de la qualité des produits, ou bien superviser plusieurs cellules de production en même temps.
7. Réaliser une analyse de risques
Enfin, en parallèle de la conception, une analyse de risques doit être effectuée. Elle assure la sécurité du futur équipement et son caractère collaboratif. Celle-ci consiste en une évaluation exhaustive de chaque risque possible. Des mesures peuvent ensuite être prises pour les éliminer ou les mitiger jusqu’à atteindre un niveau acceptable.
« Par exemple, dans le cadre du développement de la solution d’emballage en fin de ligne, on a conçu une relâche des bouteilles sans pédale pour réduire les risques associés au fait de lever son pied ou de trébucher sur les appareils au sol », indique Sébastien Cloutier.
Après avoir franchi ces sept étapes, vous aurez sans doute en main un concept pouvant être comparé à votre situation actuelle. Vous permet-il d’atteindre votre objectif? Si oui, dans quelles conditions avez-vous envie de passer à l’action? L’automatisation de tâches manuelles sans valeur ajoutée agit souvent comme point de départ vers de nouvelles façons d’aborder le travail de production. Votre équipe se sent-elle confiante? Avez-vous un groupe favorable au changement? On vous parie qu’une fois la petite étincelle allumée, les idées visant à intégrer de plus en plus de nouvelles technologies ne manqueront pas.
Auteure : Marie Michèle Lemay
Communication, talent et culture
Radius Automatisation industrielle
[email protected]
Saviez-vous qu’ESM offre des contributions non remboursables (subventions) pour vos projets de robotisation ou de numérisation? Communiquez avec nos conseillers pour en savoir davantage.